Is your pump making popping sounds or noise that resembles pumping marbles? You might be dealing with cavitation, a serious issue that can lead to increased energy consumption, excessive noise, and severe pump damage.
Understanding Pump Cavitation Causes & Effects
Cavitation occurs when bubbles form in the liquid around a pump’s impeller due to areas of low pressure. When these bubbles collapse, they create powerful shockwaves inside the pump that can damage both the impeller and pump housing.
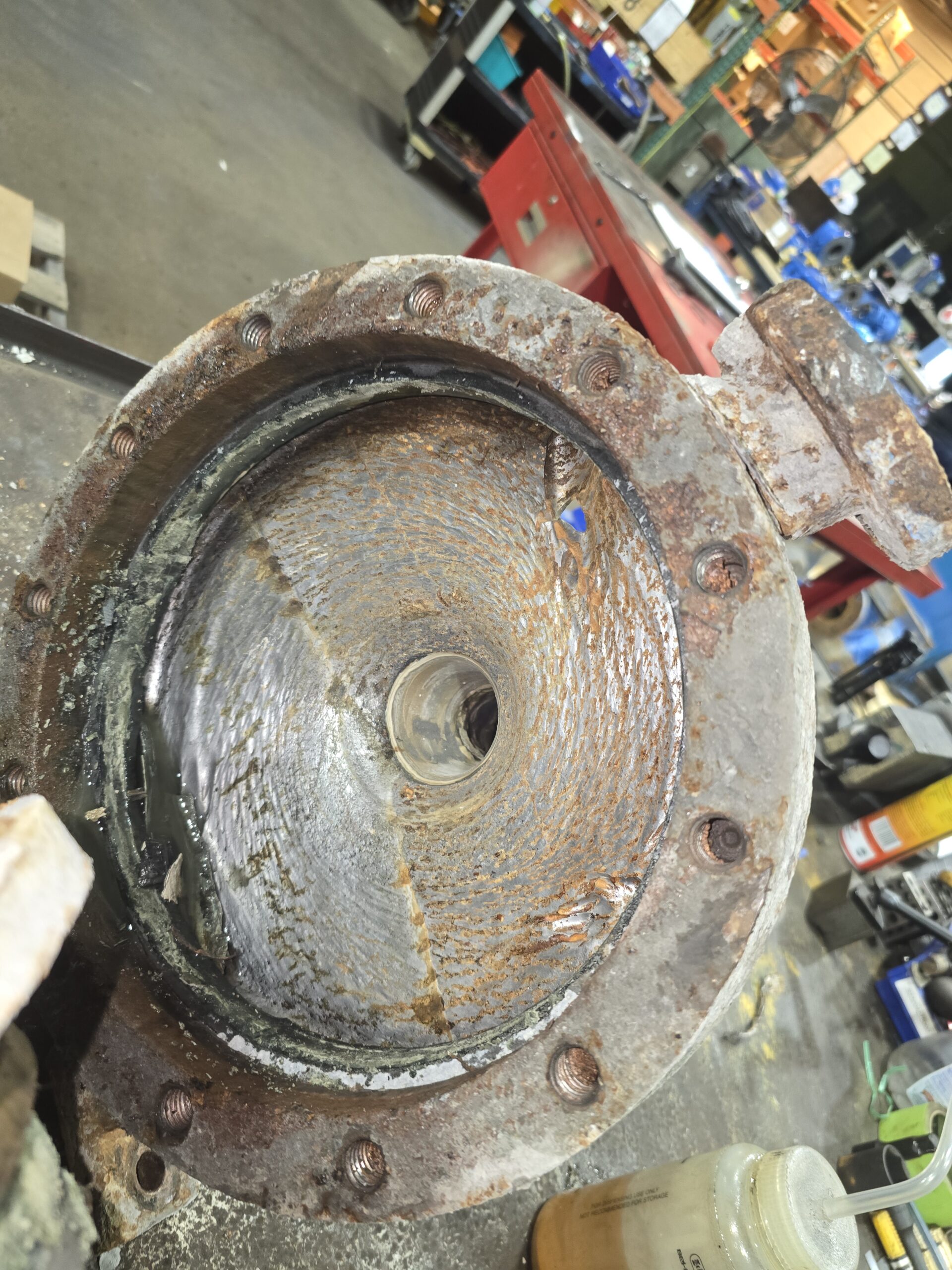
The Consequences of Untreated Cavitation:
- Pump housing failure
- Impeller destruction
- Accelerated seal and bearing wear from excessive vibration
- Increased power consumption
- Reduced flow and pressure performance
Two Types of Cavitation
1. Suction Cavitation
Suction Cavitation occurs under low pressure or high vacuum conditions when the pump isn’t receiving adequate flow. Bubbles form at the impeller’s eye and implode against the impeller face when they reach the discharge side. The damage appears as sponge-like deterioration around the impeller’s eye.
Common causes:
- Blocked filters or strainers
- Pipe blockages
- Operating too far right on the pump curve
- Suboptimal piping design
- Inadequate suction conditions (NPSH issues)
2. Discharge Cavitation
Discharge Cavitation happens when discharge pressure is extremely high or when the pump operates below 10% of its best efficiency point (BEP). The fluid recirculates inside the pump, creating high-velocity flow between the impeller and housing. This forms a vacuum that creates and implodes bubbles, potentially leading to broken impeller shafts.
Common causes:
- Discharge pipe blockages
- Clogged filters or strainers
- Operating too far left on the pump curve
- Poor piping configuration
How to Avoid Pump Cavitation
To address cavitation issues:
- Inspect Filters and Strainers Regular cleaning and maintenance prevent pressure imbalances that lead to cavitation.
- Monitor Pump Performance Use pressure gauges and flowmeters to ensure operation at the best efficiency point. Running outside this range can cause recirculation, heat buildup, vibration, and reduced efficiency.
- Optimize Pipe Design Avoid designs that trap air (like inverted “U”s) or create turbulence (such as 90° bends near the pump). These features can trigger suction problems and cavitation.
With proper attention to pump sizing, pipe design, and regular maintenance of filters and strainers, you can significantly reduce the risk of cavitation damage to your pumping system.
Think Your Experiencing Pump Cavitation?
Our team of on-site engineering staff can inspect your equipment and offer solutions to fix pump cavitation. Contact our team today to get started.