In honor of Earth Day (& month) we asked our customers what questions they had regarding their pump applications and how to make them more sustainable. So here are the answers you have been waiting for!
How do I find out if my pump is operating at BEP?
Choosing more efficient pumps are not only more environmentally-friendly but they can also be big money-savers in terms of significantly lowering your energy costs. So how do you know if your pump is operating at BEP?
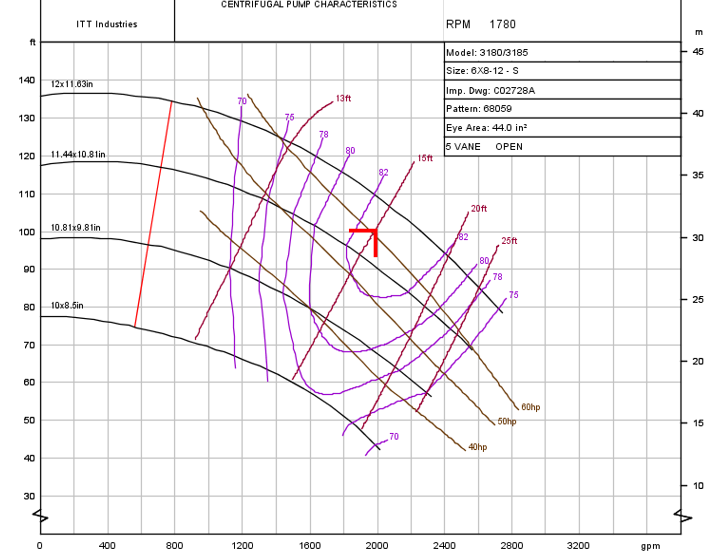
The short answer: check your inlet and outlet pressures, calculate total dynamic head, and check the curve. Need some assistance? We can help.
The long answer: Pump users should care about the Best Efficiency Point (BEP) and where their pump is running because BEP is the point at which the pump operates with the highest efficiency.
Operating a pump either out our back on the curve, away from BEP, results in:
- Reduced efficiency
- Increased energy consumption
- Premature wear and tear on the pump
All of this can lead to higher operating costs, increased maintenance and repair expenses, and reduces reliability.
Do variable speed drives really save energy?
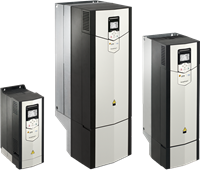
Traditionally, pumps have been designed to operate at a fixed speed to meet the peak flow requirements of the system. This means that the pump is often running at a higher capacity than is needed, or may be throttled back using a valve to keep the pump from operating too far out on its curve.
The affinity laws tell us that power consumption is proportional to the cube of the ratio of the speeds, so eliminating throttling and reducing the head by slowing down a pump can offer a significant energy savings, often with a short payback time for the investment in a drive.
Learn more about getting the most value out of your variable speed drives in our article in Pumps And Systems.
Are variable speed drives the ONLY way to save energy?
Not at all! Energy savings starts with good pump specifications. The most efficient pump is one running
at full speed and at the Best Efficiency Point.
Oversized pumps impellers can be trimmed to reduce the need for throttling and horsepower. Reducing the flow rate though a pump can also save significant energy. Specifying for just the required flow, closing unnecessary bypasses, and running at the flow rate required by the process without significant excess flow can all significantly save energy.
Old, worn pumps can also consume significantly more energy than new or refurbished pumps. According to the department of energy, pumps can lose as much as 30% of their efficiency as they age. Regular maintenance and overhauls when indicated can return pumps to like-new condition, offering significant savings. Check out our service and repair capabilities here.