This guide reviews critical considerations when installing metering pumps, and will discuss how chemical metering systems can ensure successful installations. We offer this guide as a starting point; Iif you have specific chemical metering questions, our team of applications engineers can help. Contact us here to get started.
What Is a Chemical Metering System?
A chemical metering system integrates a metering pump with all the accessories, instruments, and controls to accurately pump a precise volume of liquid at a specified rate. Purchasing a metering system, rather than a standalone pump, simplifies the design process and procurement, and allows faster installation and start-up because the system arrives pre-built and tested.
A chemical metering pump, also known as a metering pump or dosing pump, is a pump that’s primary purpose is to dispense a precise volume of liquid during a specified time period. Metering pumps are used for a wide variety of applications including dispensing of sodium hypochlorite, sodium hydroxide, methanol, ethanol, ferric chloride, dyes, and other additives.
8 Steps to a Successful Metering System
1. Choose The Right Pump For Your Application
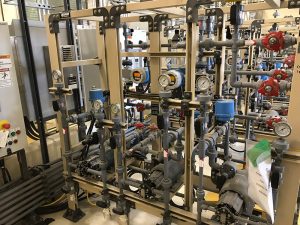
Metering pumps come in many styles, including:
- Hydraulically actuated diaphragm pumps
- Peristaltic pumps
- Piston pumps
- Progressing cavity pumps
- Seal-less magnetically driven gear or standard sealed gear pumps
- Air operated diaphragm pumps, and more
This means choosing a trusted application engineer to consider the requirements of both your plant and application is vital for choosing the right one. An application engineer will take the following into consideration when choosing a suitable style of pump:
- Flow Rate: Max, Min, and Typical flow rates
- Suction Conditions
- Discharge Pressure
- Required Accuracy
- Process Fluid: Chemical compatibility, viscosity, off gassing, safe handling
- Ease of Maintenance, availability of parts.
- Pump Availability
It is also important to consider maintenance requirements when vetting an appropriate pump. Metering pumps vary widely in their complexity and in the skill and time required to maintain the pump. If you’re looking for a style of pump that is easier to maintain, be sure to mention that to your application engineer. They can help you understand the benefits and tradeoffs of specific types of pumps, and ultimately find a pump that is a good match for your application and your maintenance resources. It is also helpful to know if your pump supplier can support you with maintenance and repair services.
2. Pay Careful Attention To Your Suction Conditions
The most common cause of metering pump trouble is poor suction conditions. Undersized piping can starve the pump, and oversized or excessively long pipe or routing with high points may never prime or may lose prime due to chemical off gassing. Pulsating flow can also significantly change the sizing calculation for suction piping and may require suction side pulsation dampers for some installations.
3. Install Components Per The Manufacturer’s Recommendations
Every component in your metering system needs to be installed per the manufacturer’s instructions. For pumps, this means paying attention to acceptable suction conditions and NPSH, remembering to accommodate high pressure if present, and consider possible off gassing, venting, and flushing. Other supporting components need to be properly installed as well to ensure the system, as a whole, functions properly.
4. Check The Route And Installation Location
Nearly all equipment needs to travel through a building before installation. Check the path for doors, narrow passages, hatches, hoists, stairs, and any point that may make moving the equipment into place difficult. Careful system design can accommodate nearly any routing limitation.
Check the final location and consider these questions:
- Will the installer have to work in a tight area?
- Is the area safe for installation activities?
- Is quick changeover needed to avoid down time or minimize installation costs?
The answers to these questions can help you determine if a system or standalone pump alone is right for you. Be sure to let your system designer know all your space limitations, before, during, and after installation.
5. Consider Maintenance

All machines, including pumps require some monitoring and maintenance. Be sure the system is designed to allow your team to safely maintain the pump and other components requiring regular maintenance, such as pulsation dampers. Systems should include proper vent and drain connections and suitable flushing connections for the application, and may need lockable isolation valves and/or block and bleed arrangements.
6. Make Sure To Include The Right Components – In The Right Locations
Depending on the selected pump and application, you may need relief valves, back pressure valves, isolation valves, strainers, calibration columns, instruments such as flow or pressure transmitters, control valves, pulsation dampers, pressure gauges with isolators, and more. All these must need careful selection to be compatible with the pumped chemical. Further, when selecting the order and location of these components, be sure to install the components so they work together efficiently. For example: control valves should be installed downstream of flow meters rather than immediately upstream to avoid disrupting flow and reducing the accuracy of the flow meter.
7. Consider The Operator
How will they control the pump? Metering Pump controls may be purely mechanical, or may use variable speed drives and sometimes a PLC. Controls should be designed to make the operator’s regular adjustments and monitoring activities as easy as possible. Will the control system need to be set up in the field? Can the operator easily access valves, pressure gauges, and other components regularly used to operate and monitor the system? Especially in systems with multiple pumps, the design of the pump systems to allow operator access must be done carefully, or your operators may end up living with years of headaches.
8. Consider Redundancy
Chemical metering systems are commonly set up with two pumps, each sized for 100% of the maximum demand flow rate, or three pumps each sized for 50% of the maximum demand to allow higher turndown in flow rate because the pumps are smaller. Critical systems can also be designed with redundant controls or mechanical overrides, installed spare pumps that can be valved in as needed, sometimes “swinging” between multiple discharge points. Other strategies to maximize reliability and redundancy in metering pump systems include drain ports with hose fittings used as back-up supply ports from a tote in the event of a tank failure, electrical receptacles on motors can allow a failed pump to be “unplugged” and rapidly swapped with a spare, and metering pumps can be chosen in a rapidly rebuildable style allowing most pump repairs to be completed in a few minutes with parts from an easily stored kit.
Contact Us!
Geiger offers custom and standard chemical metering systems in addition to stand-alone pumps and accessories, so you can choose the right solution for your installation. Complete chemical metering systems arrive at your facility assembled with everything you need for a complete functional system, factory tested and ready to go.
Contact our team to get started